When it comes to setting up a solar inverter (for any type), the engineer/installer have to ask for certain features or you can say the qualities to the manufacturer because lacking of these feature in a inverter causing the system in-efficient. So in this post, i'll discuss about those particular features that we are looking for at the time of purchasing/installing solar inverter.
1. Maximum Power Point Tracking
Solar inverters use maximum power point tracking (MPPT) to get the maximum possible power from the PV array. Solar cells have a complex relationship between solar irradiation, temperature and total resistance that produces a non-linear output efficiency known as the I-V curve. It is the purpose of the MPPT system to sample the output of the cells and determine a resistance (load) to obtain maximum power f or any given environmental conditions. Essentially, this defines the current that the inverter should draw from the PV in order to get the maximum possible power (since power equals voltage times current).
In this image you can see that if we use a inverter which works without an MPPT algorithm, then the system become in-efficient or in other words there will be losses in utilizing the solar power. But we use an inverter which works on a MPPT algorithm thenthe utilizing of power is far better.
Now, we should know about the Fill-Factor. what is Fill Factor or FF?
The fill f actor, more commonly known by its abbreviation FF, is a parameter which, in conjunction with the open circuit voltage and short circuit current of the panel, determines the maximum power from a solar cell. A solar micro-inverter in the process of being installed . The ground wire is attached to the lug and the panel's DC connections are attached to the cables on the lower right. The AC parallel trunk open circuit voltage and short circuit current of the panel, determines the maximum power from a solar cell. Fill f actor is def ined as the ratio of the maximum power f rom the solar cell to the product of Voc and Isc.
There are three main types of MPPT algorithms: perturb-and-observe, incremental conductance and constant voltage. The first two methods are often referred to as hill climbing methods; they rely on the curve of power plotted against voltage rising to the left of the maximum power point, and falling on the right.
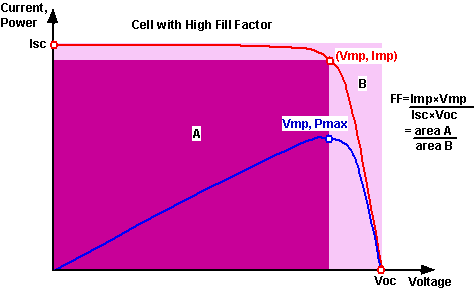 |
MPPT With FF Display |
A general algorithm of MPPT shown here.
2. Anti-Islanding Protection

In the event of a power failure on the grid, it is generally required that any grid-tie inverters attached to the grid turn off in a short period of time. This prevents the inverters from continuing to feed power into small sections of the grid, known as "islands". Powered islands present a risk to workers who may expect the area to be unpowered, but equally important is the issue that without a grid signal to synchronize to, the power output of the inverters may drift from the tolerances required by customer equipment connected within the island.
Detecting the presence or lack of a grid source would appear to be simple, and in the case of a single inverter in any given possible physical island (between disconnects on the distribution lines f or instance) the chance that an inverter would f ail to notice the loss of the grid is effectively zero. However, if there are two inverters in a given island, things become considerably more complex. It is possible that the signal from one can be interpreted as a grid feed from the other, and vice versa, so both units continue operation. As they track each other's output, the two can drift away from the limits imposed by the grid connections, say in voltage or frequency.
There are a wide variety of methodologies used to detect an islanding condition. None of these are considered fool-proof , and utility companies continue to impose limits on the number and total power of solar power systems connected in any given area. However, many in-field tests have failed to uncover any real-world islanding issues, and the issue remains contentious within the industry.
3. Redundancy
Redundancy is one of the main reason string inverters and microinverters are chosen instead of central inverters because in case of failure a smaller part of the system will be affected. String inverters have the added benefit of being a standard readily available commercial component which means it’s possible to let a local installer or facility manager exchange the inverter if necessary; also extra inverters can be kept in stock for quick exchange. Conversely, service contracts should be offered with central inverters and they should be serviced only by trained experts.
4. Total Harmonic Distortion
The total harmonic distortion, or THD, of a signal is a measurement of the harmonic distortion present and is defined as the ratio of the sum of the powers of all harmonic components to the power of the fundamental frequency. THD is used to characterize the linearity of audio systems and the power quality of electric power systems.
So, it is desired that a inverter should have feature to cancel out the most of the higher harmonics as possible
.
When the input is a pure sine wave, the measurement is most commonly the ratio of the sum of the powers
of all higher harmonic
frequencies to the power at the first harmonic, or fundamental
, frequency.
which can equivalently be written as

if there is no source of power other than the signal and its harmonics.
Measurements based on amplitudes (e.g. voltage or current) must be converted to powers to make addition of harmonics distortion meaningful. For a voltage signal, for example, the ratio of the squares of the
RMS voltages is equivalent to the power ratio:

where Vi is the RMS voltage of ith harmonic and i = 1 is the fundamental frequency.
THD is also commonly defined as an amplitude ratio rather than a power ratio,
[3] resulting in a definition of THD which is the square root of that given above:

This latter definition is commonly used in audio distortion (percentage THD) specifications. It is unfortunate that these two conflicting definitions of THD (one as a power ratio and the other as an amplitude ratio) are both in common usage.
So, it is desired that a inverter should have feature to cancel out the most of the higher harmonics as possible.
Follow me on Academia.edu
About the AuthorAmrit Mandal is a final year B.tech (EE) Student, Admin of this blog. He likes to work in the renewable energy field-specially in solar energy field.
Follow Us on Twitter
#REnergy_Blog
REnergy